はじめに
前回の記事で粘土型を利用したポリエステル系のホールド作りに成功したので、今回は応用編としてスタイロフォームを使ったホールド作りに取り組もうと思う。形状としては、「市場にないピンチボード」をテーマに作成してみた。また、樹脂も「ポリエステル」と「ポリウレタン」の2種類を試してみた。
準備
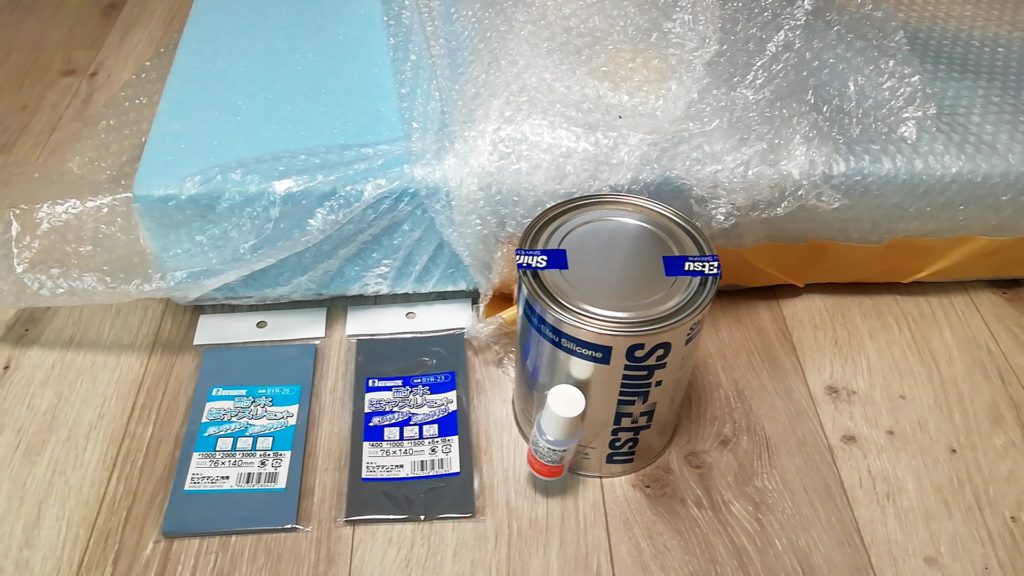
◆型材料
・スタイロフォーム(デュポン・スタイロ㈱)
・KE-17(信越化学工業㈱)、硬化剤付き
・プラスチック容器(型が入る大きさと深さのもの)
◆ホールド材料
ポリエステル系
・不飽和ポリエステル樹脂(インパラ、硬化剤付き)
ポリウレタン系
・ウェーブレジンキャストEX(A液、B液)
◆補助
・電動ドライバー(ビス、ボルト穴開け用)
・一般工具(ペンチ、ドライバなど)
・割りばし(液かき混ぜ用)
・カッター(切削用)
・鋸(あったら)
・彫刻刀(あったら)
・ナイフor包丁(切断用)
・サンドペーパー
・計量カップ(500mL)
◆固定
・ボルト
・ビス
作業
・マスク
・手袋or軍手
※不飽和ポリエステル樹脂とか硬化剤ってなに!?って方は以下の記事を参考になさってください。
ホールド材料 専門用語解説
シェイプ
①スタイロフォームを好みの形状にシェイプする。
②ボルト穴(とビス穴)をあける
③紙やすりなどで軽くきれいに整える
※床が傷つくので下に段ボールなどを敷きながら作業した方がいいです。
※微細な粉塵(マイクロパウダー)が舞うので最低限マスクは必須です。
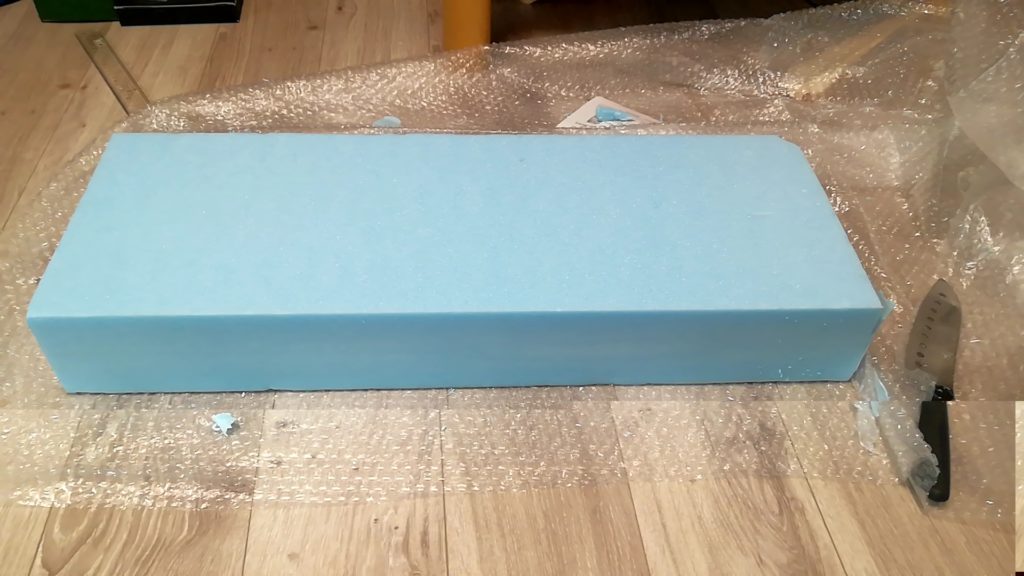
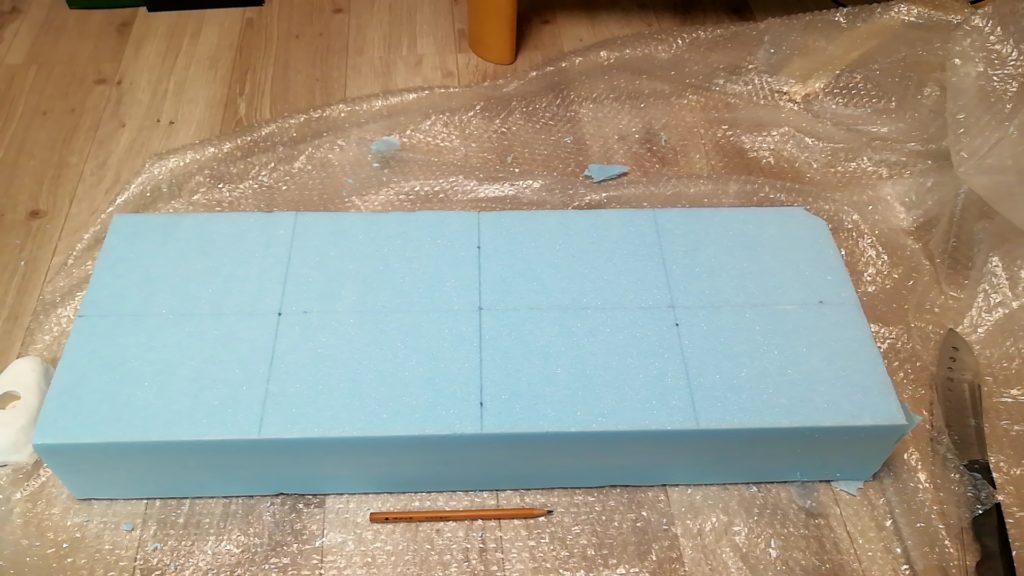
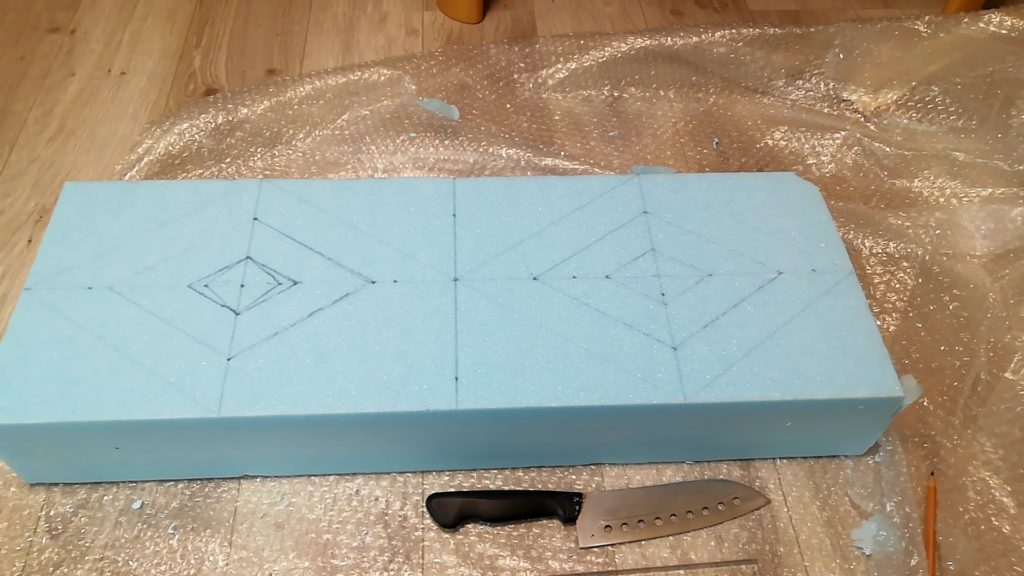
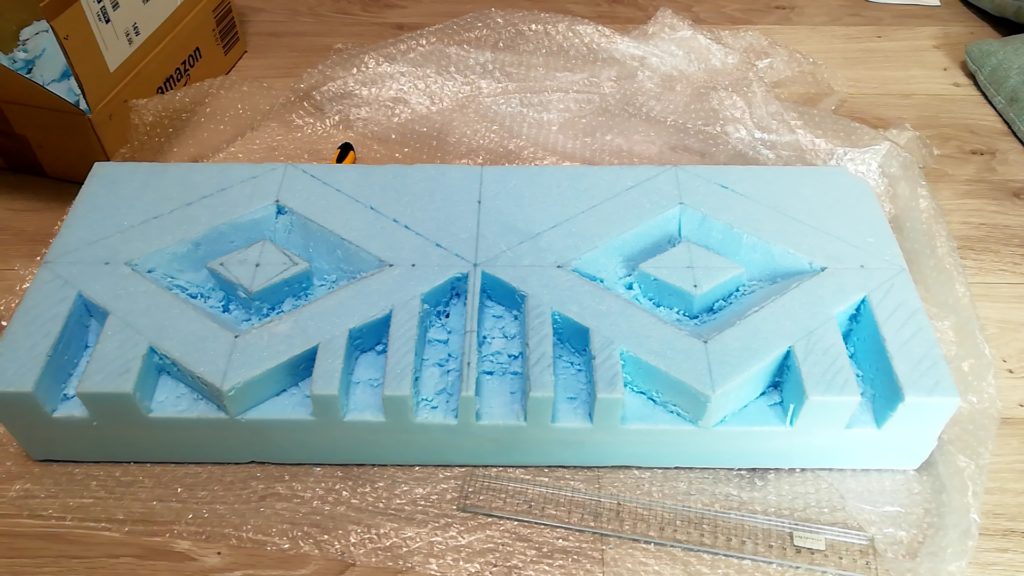
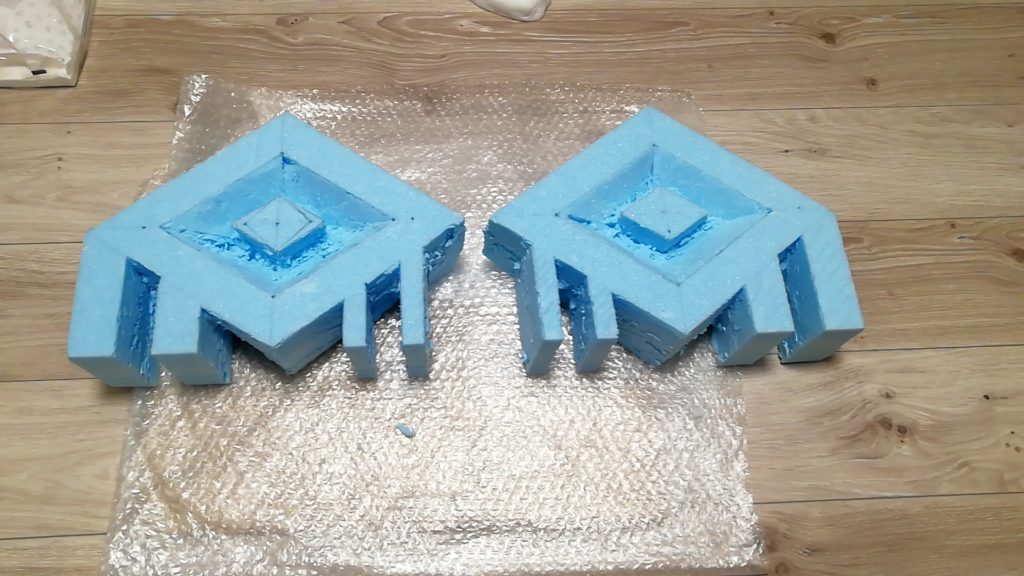
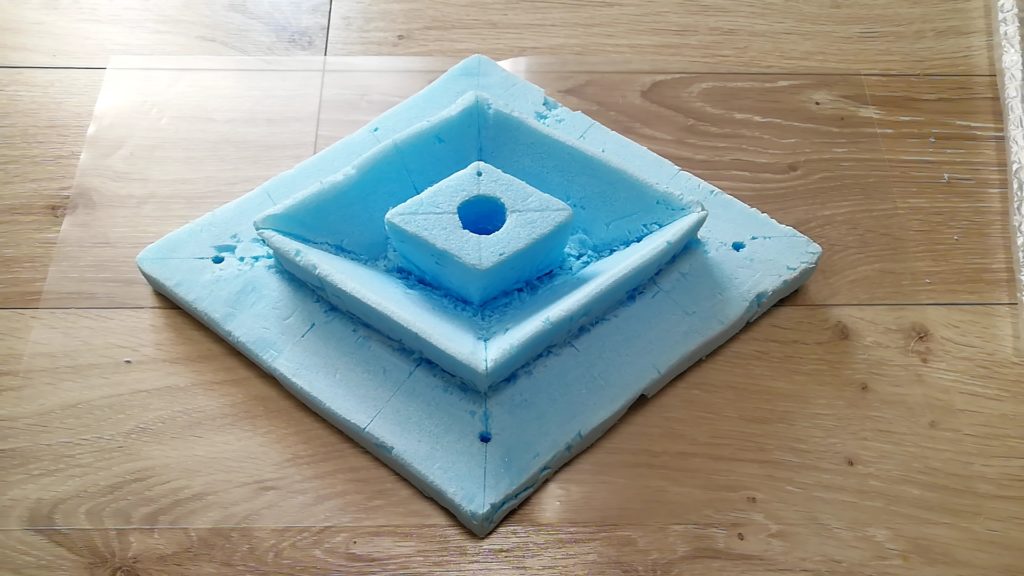
特に何も考えてなかったので、その場の成り行きで作っていったが、最終的に三重構造のひし形に落ち着いた。beastmakerみたいなのを最初は作ろうとしていたが、カチとは違い、ピンチはスペースをとるので同じようには作れなかった。そこで削りながらふと思いついたのが上のシェイプ。Black Diamondのマークみたいで個人的には気に入っている。イチオシポイントはこのホールドだけでピンチの持ち方が何通りもあるところ。
一点、気がかりなのは「穴」が上手く型取れるかどうかということ。特にボルト穴はワッシャーサイズのビットがなかったのでかなりやっつけで作ってしまったし、ビス穴は細すぎてフォームを取り出すときに消滅しそう(笑)。また、本来はもっと余計な凹凸が少ない面になるように削るべきなのだが、カット方法が雑すぎたので復旧が難しく、ある程度やすりがけしてから次工程に移行した。
シリコーン型取り
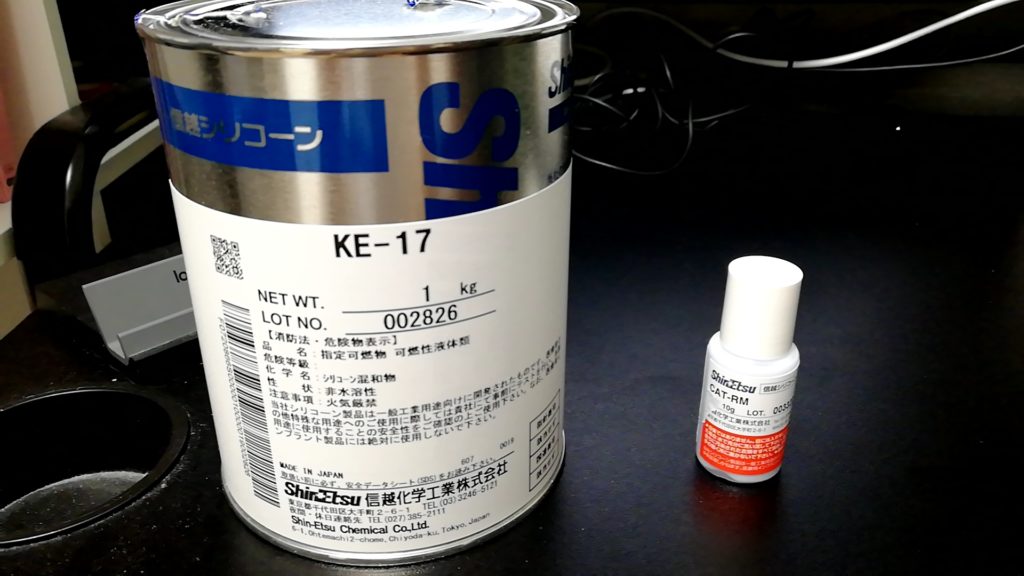
今回用いたのは信越製の硬めのシリコーンだが、正直何でもいいと思う。私は初めてだったので手堅くいこうと思い、これを選んだが。。
圧倒的に量が足りない!!
大きめのホールドだったこともあり、結局4缶も使う羽目になってしまった。3500円×4缶=14000円はエグい、というかアホ(笑)。やはり型取りシリコンは1000円~2000円/kgくらいの安いの買わなきゃだめやな。採算が合わん。
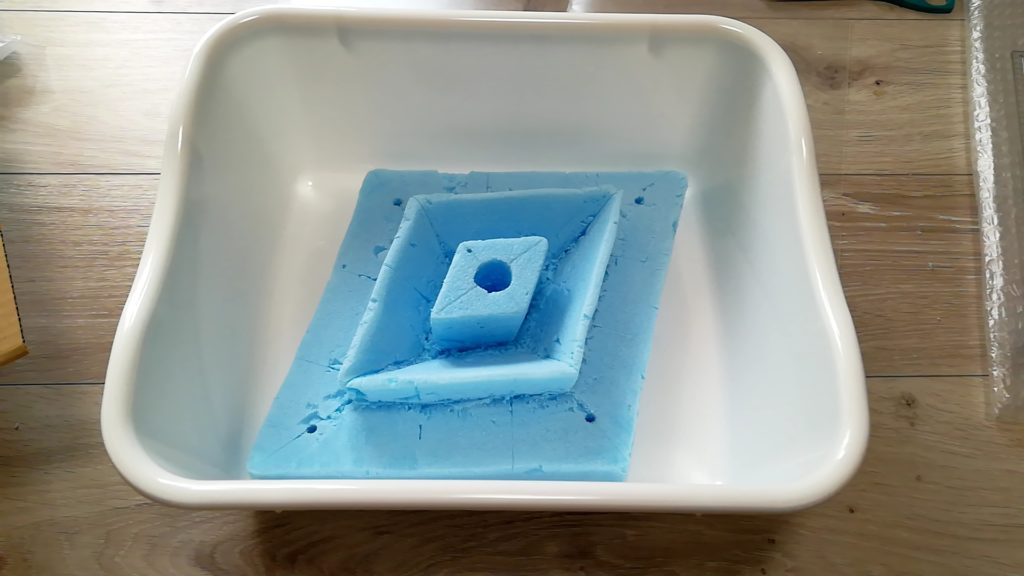
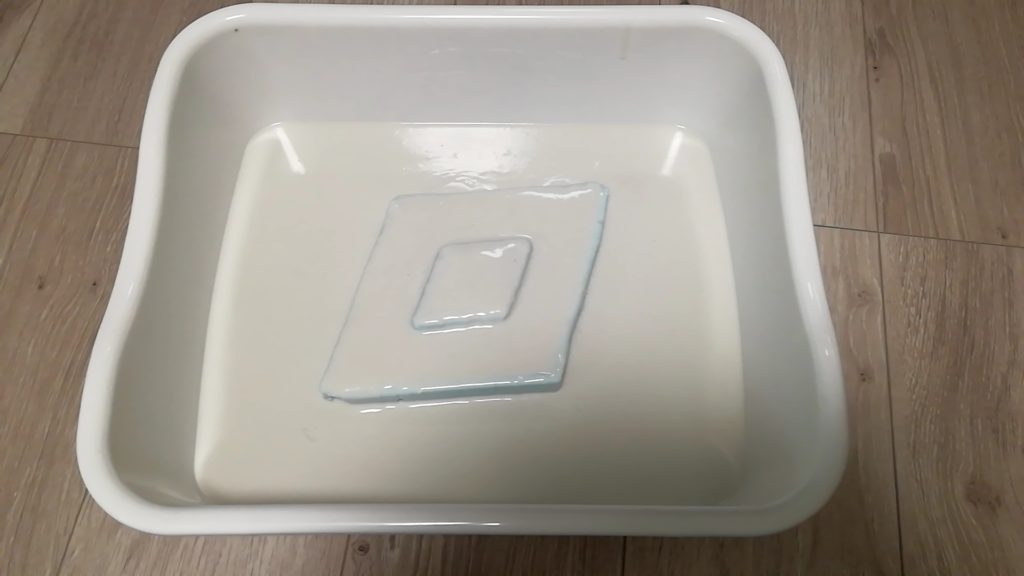
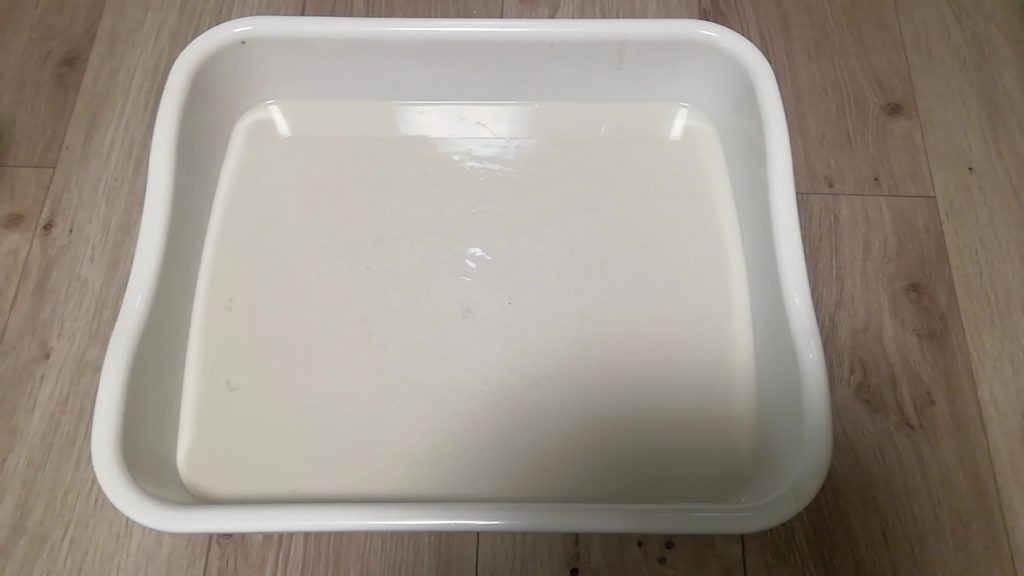
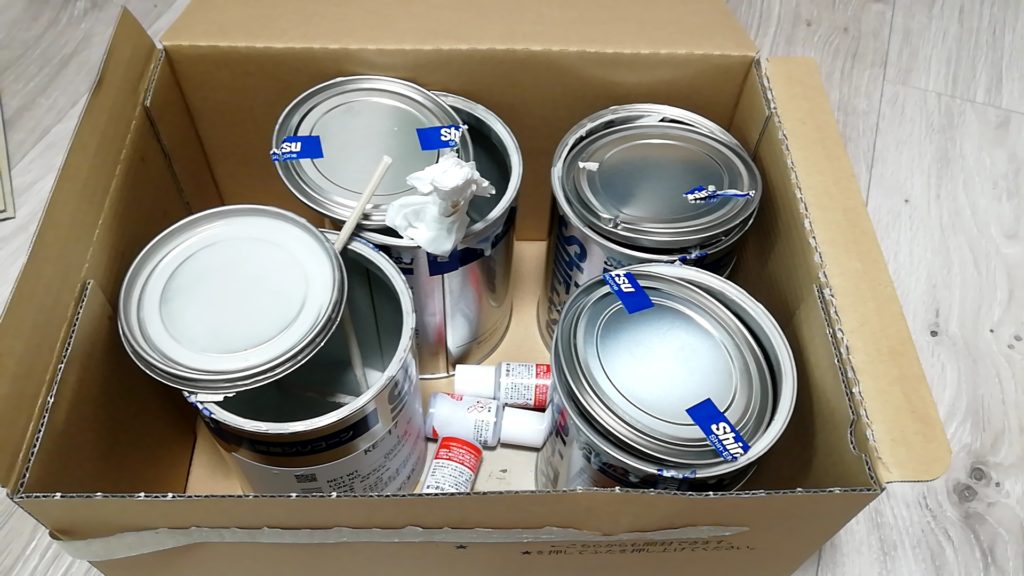
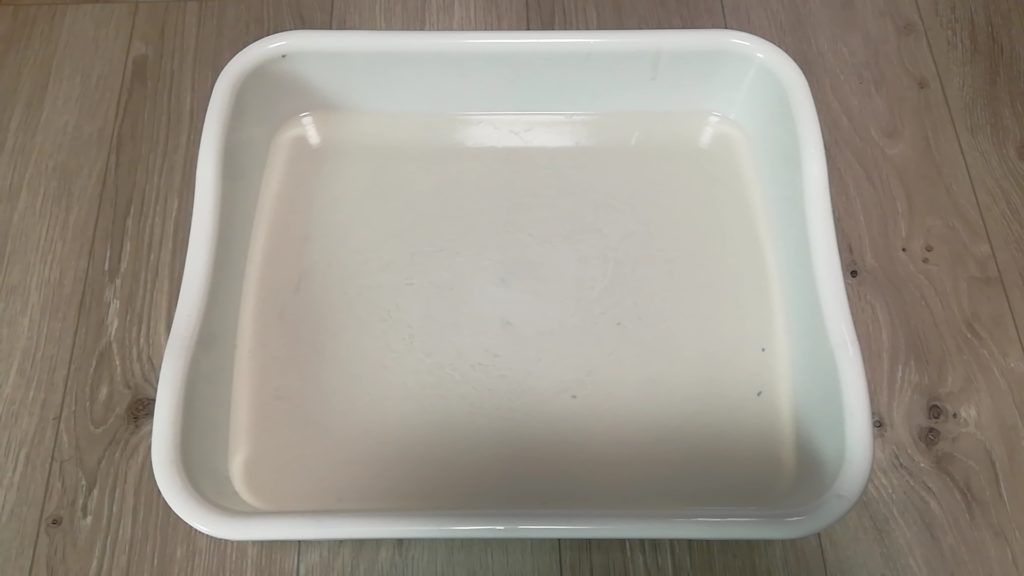
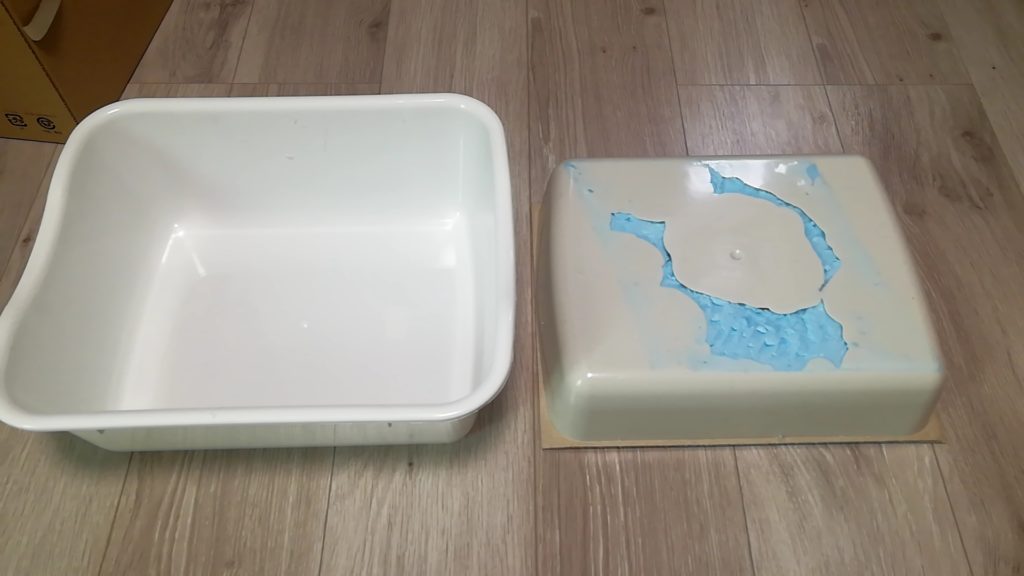
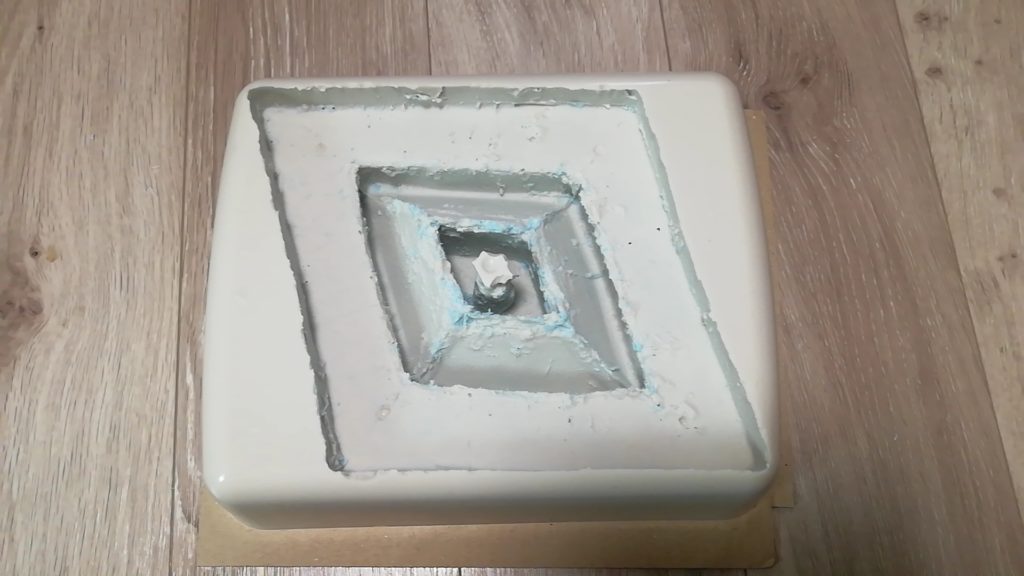
樹脂硬化(ポリエステル)
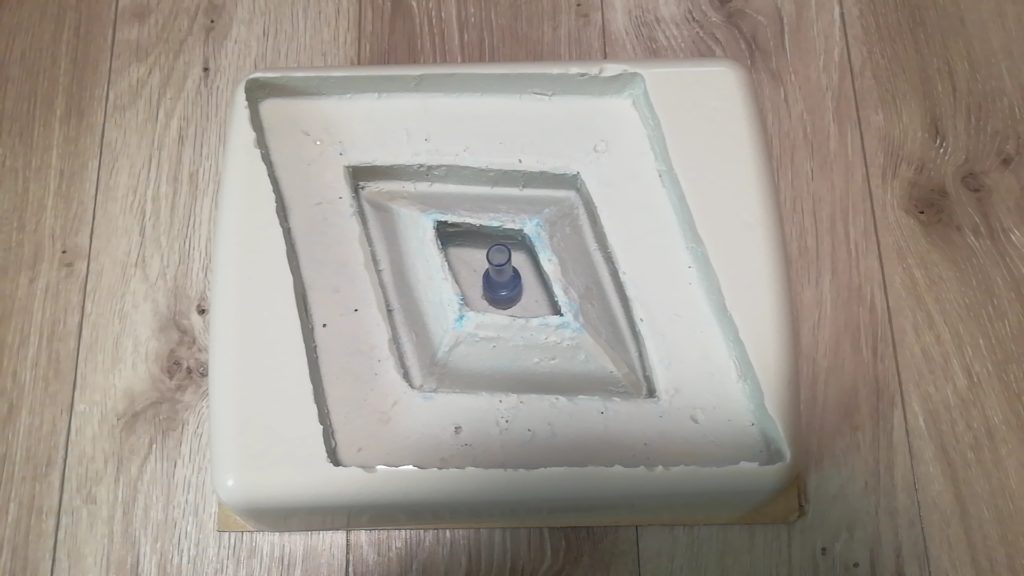
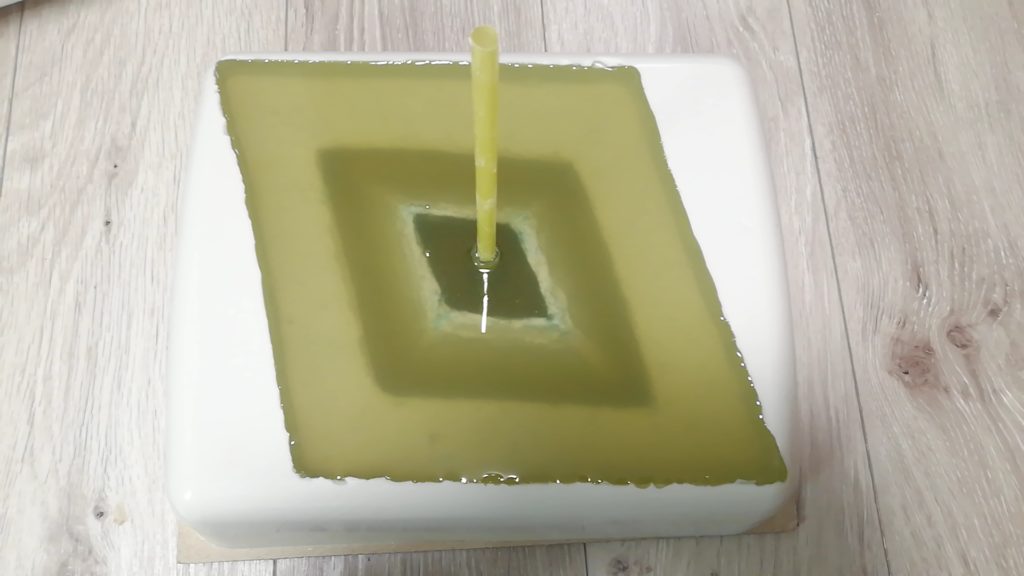
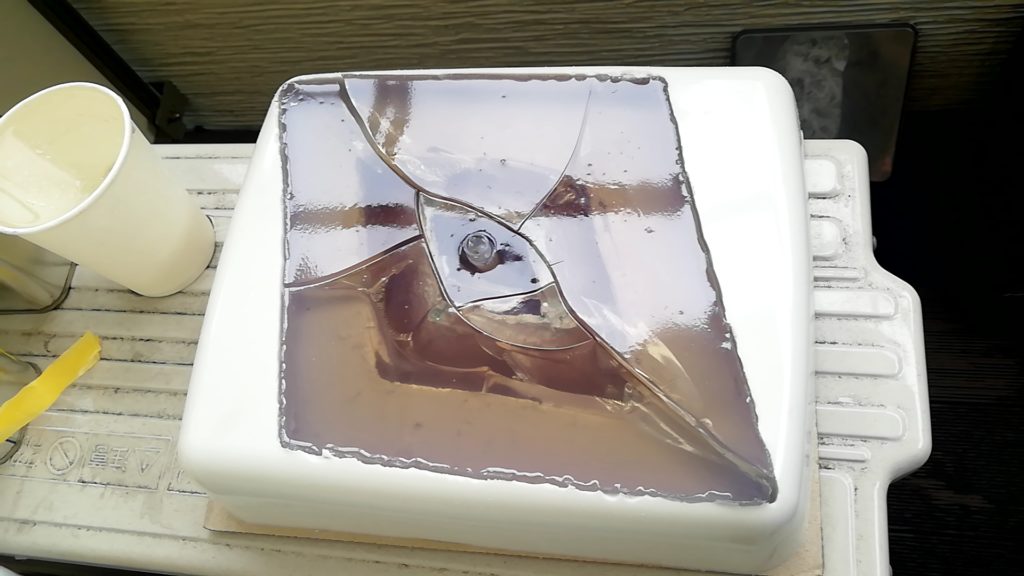
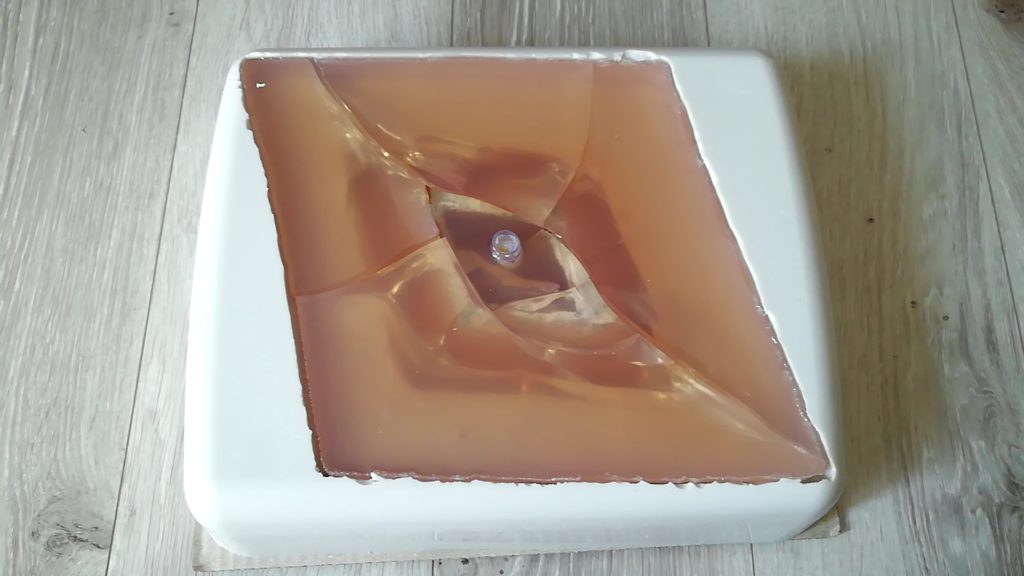
樹脂硬化(ポリウレタン)
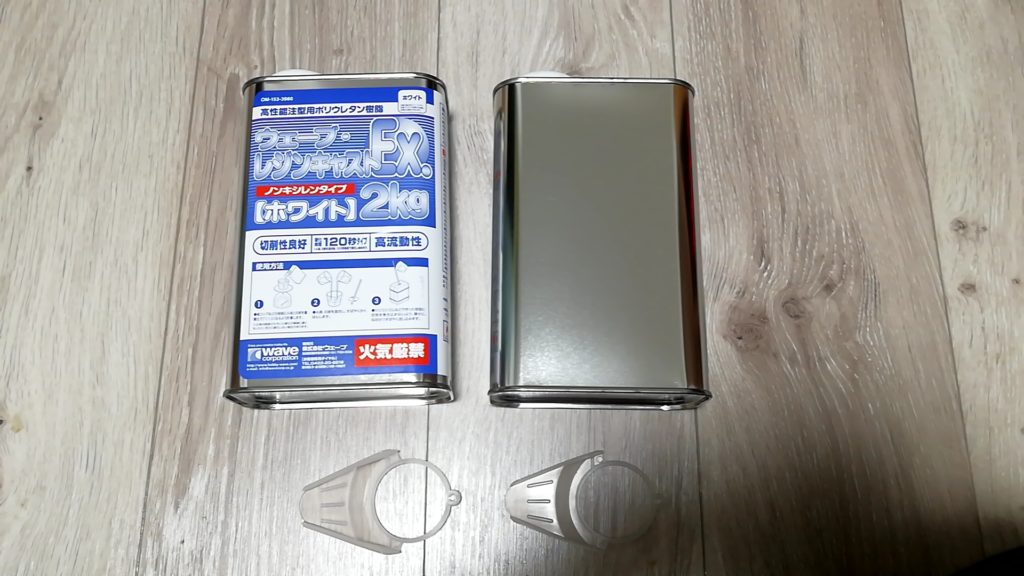
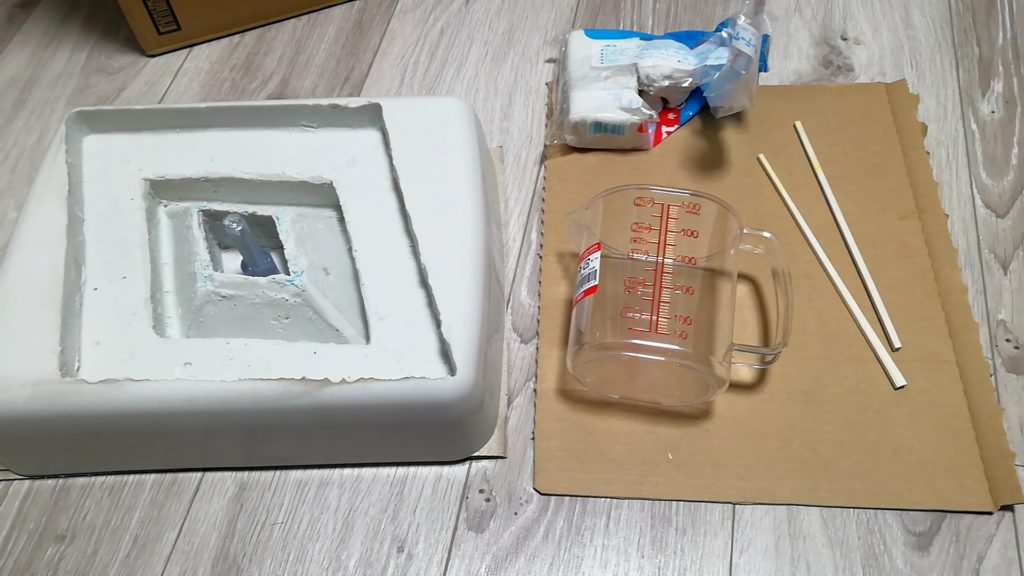
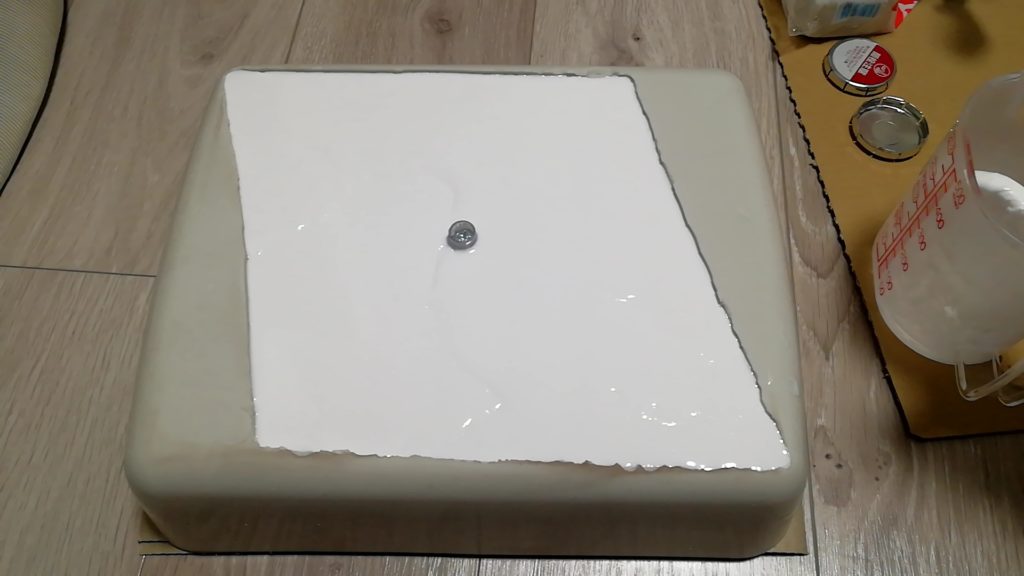
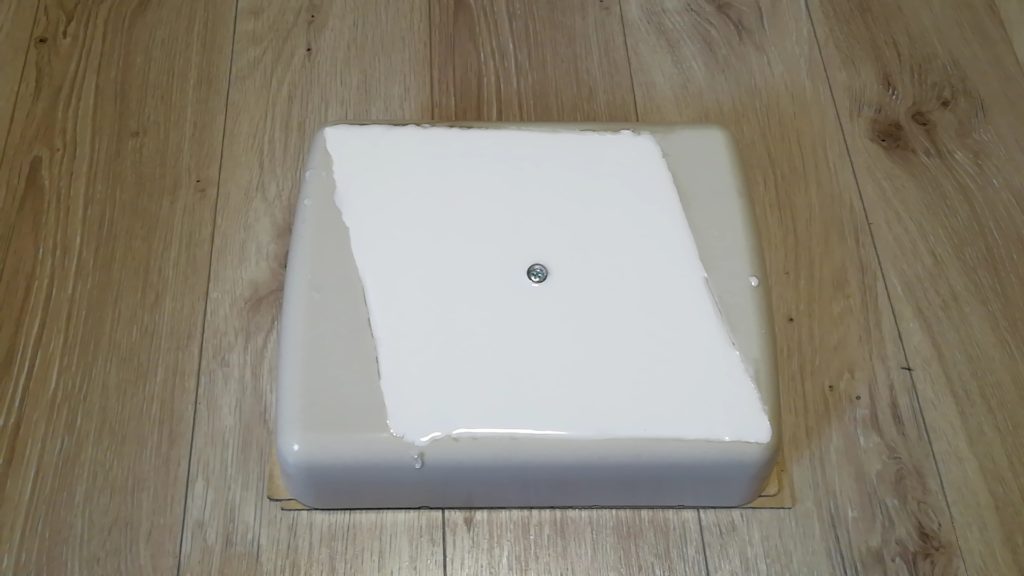
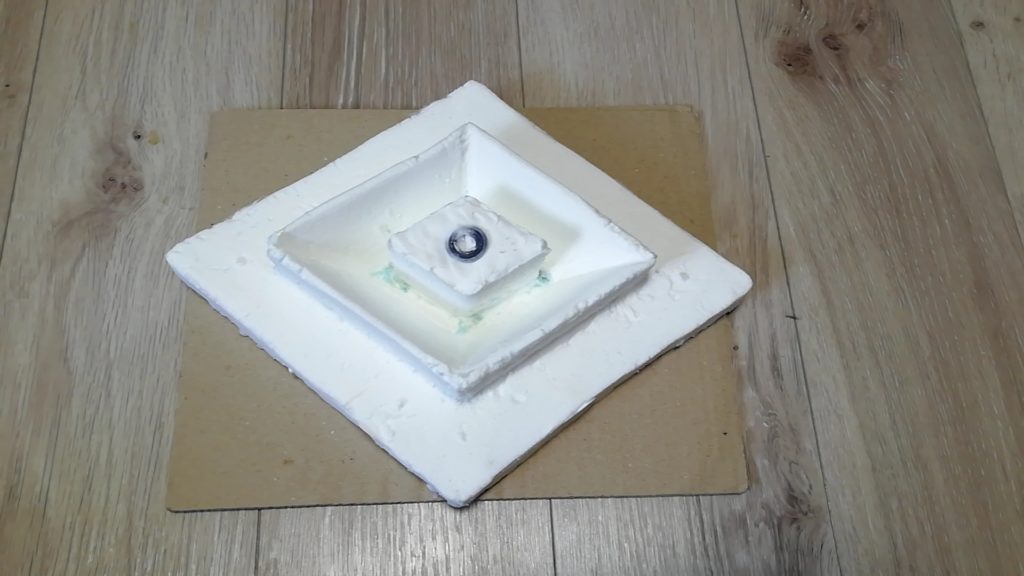
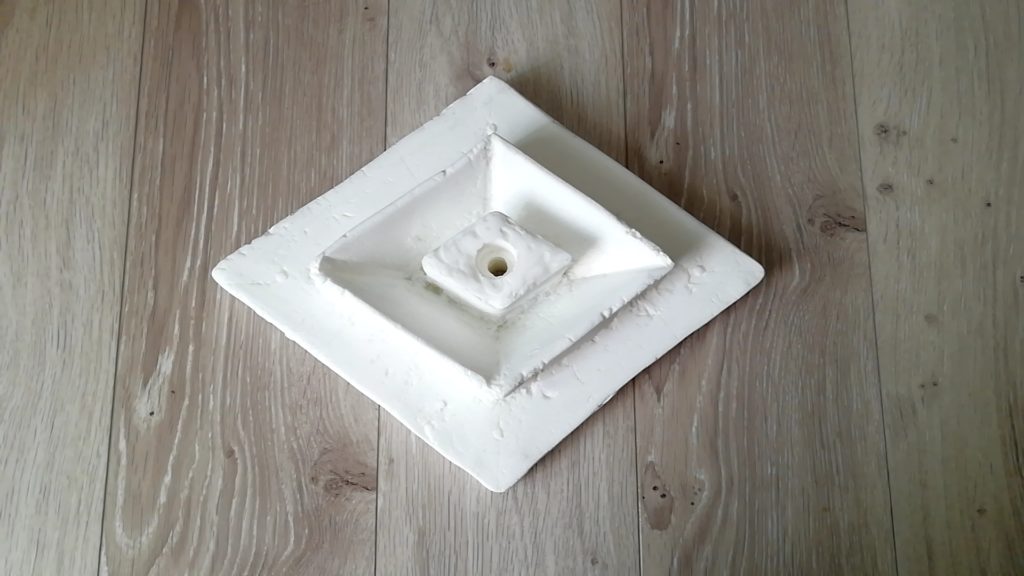
さいごに
シェイプについては、流石に粘土よりは楽でしたが細かな手作業の難しさを痛感しました。鋸がなかったので包丁を使って無理矢理カットしていたら、フォームの切断面がボロボロになってしまったうえ、やすりが入り込みにくい溝だと研磨しきれない箇所もあったので、寸法通りに綺麗に仕上げるのが難しかったです。もう少し小さなホールドだったら多分なんとかなったでしょうが、今回のような大きめのホールドはどうしようもないですね笑。
シリコーン型については、使用前によくかき混ぜる必要はありましたが、信越化学製なだけあってしっかりした素材で、割けたり潰れたりすることはなく、型として十分な強度および柔軟性を有していました。流し込む容器も100均で売っているようなプラ製でもシリコーン硬化後にスルっと抜けてくれて助かりました。また、硬化後の樹脂の取り出しやすさも良好でした。ただ、3500円/kgと少し高額なのでもう少し安いものの方がいいかもですね。
樹脂については、今度から家で作るとしたら圧倒的にポリウレタンですね。ポリエステルは臭いので家の中ではかなり扱いづらいですし、大きなものを作ろうとすると体積収縮の影響を強く受けることが判明しましたので。しかし、それぞれの樹脂の材料物性については調べ切れていないところがあるので、後々データでも比較してみたいと思います。
◆ポリエステル樹脂
臭気:スチレンや溶剤等の蒸気がかなり臭い
硬化速度:遅い(1日程度)
体積収縮:あり
◆ポリウレタン樹脂
臭気:ほとんど匂わない
硬化速度:速い(数時間)
体積収縮:ほぼなし
また、樹脂だけでは触感が物足りないという方は、表面のフリクション調整として、砂系の粒子をまぜてみても面白いかもしれません。通常通り硬化するかは粒子の種類や配合率、含水率にもよりますし、しっかりと表層に出てきてくれるかもやってみなければ分からないので、一概に成功するとは言い切れませんが。
今後はこのホールドを3Dプリンタでも作ってみたいと思います。今までよりCADが少し難しそうなので勉強しながらゆるゆるやっていきたいですね。主な目的は、寸法精度の向上と軽量化です。また完成したら記事にしていきたいと思います。それでは。
コメント